Extruded silicone rubber strips and gaskets are products that are manufactured using a process of extrusion to create custom shapes and sizes. These products are made from high-quality silicone rubber material and can be designed to fit a wide variety of applications across various industries. Extruded silicone rubber strips and gaskets are commonly used for sealing and cushioning purposes in industries such as automotive, aerospace, construction, and food processing. They are known for their flexibility, durability, and resistance to extreme temperatures and harsh environmental conditions.
Why Use Silicone Rubber for Gaskets?
Using high-quality materials for extruded silicone rubber products is important for several reasons:
Durability: High-quality materials can withstand wear and tear, extreme temperatures, and environmental factors such as UV light, moisture, and chemicals, making them more durable and longer-lasting.
Performance: High-quality materials can provide better performance in terms of flexibility, elasticity, and resistance to compression set, which is the ability of the material to return to its original shape after being compressed.
Safety: Extruded silicone rubber products are used in a variety of industries, including medical and food processing, where safety is critical. High-quality materials can ensure that the product is free of contaminants and meets regulatory requirements for safety and purity.
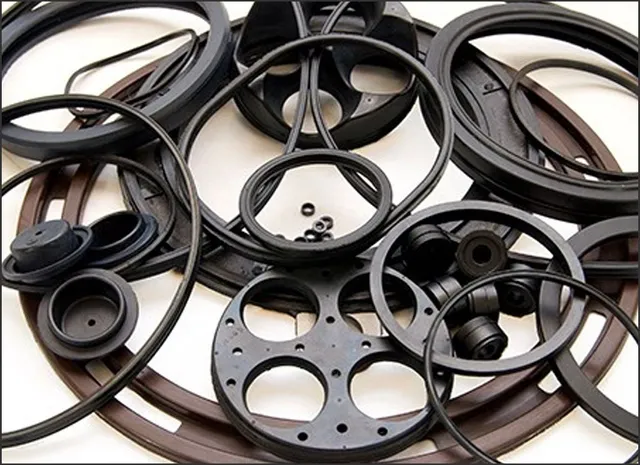
Aesthetics: High-quality materials can provide a better finish and appearance, which is important in industries such as automotive and consumer electronics.
Cost-effectiveness: While high-quality materials may cost more initially, they can provide cost savings in the long run due to their durability and performance, reducing the need for frequent replacements and repairs.
Overall, using high-quality materials for extruded silicone rubber products is essential to ensure that the products meet the required standards for durability, performance, safety, aesthetics, and cost-effectiveness.
What is Extruded Silicone Rubber?
Extruded silicone rubber is a type of rubber material that is processed using an extrusion process to form a variety of shapes, profiles, and designs. This material is a synthetic polymer made from silicon, oxygen, carbon, and hydrogen, and it is known for its excellent properties such as resistance to temperature extremes, weathering, and chemical attack.
The extrusion process begins with raw silicone rubber material in the form of pellets, which are fed into an extruder machine. The extruder consists of a barrel, which houses a rotating screw that mixes and melts the rubber material to a viscous state. The molten rubber is then forced through a die, which is a specially designed metal plate with a specific shape and size of the desired extruded product.
As the rubber is forced through the die, it cools and solidifies to the required shape, and is cut to the required length. The extruded product may then undergo additional processing, such as vulcanization, to improve its physical properties and durability.
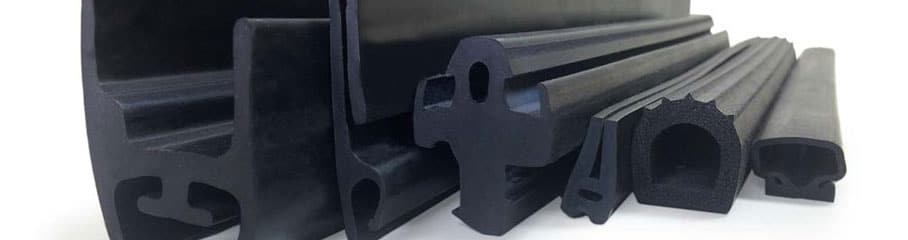
Extruded silicone rubber can be manufactured in a variety of shapes and sizes, including tubes, cords, gaskets, seals, and profiles, and can be customized to meet specific requirements of customers. The manufacturing process allows for high precision and consistency in the production of extruded silicone rubber products, making them ideal for use in various industries, including automotive, aerospace, food and beverage, and medical applications.
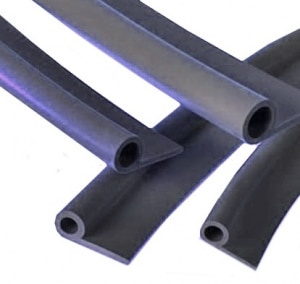
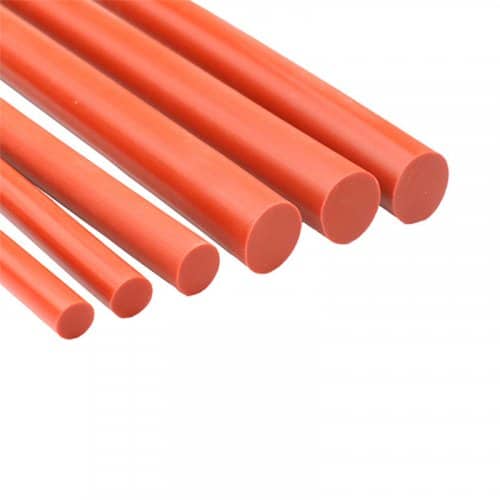
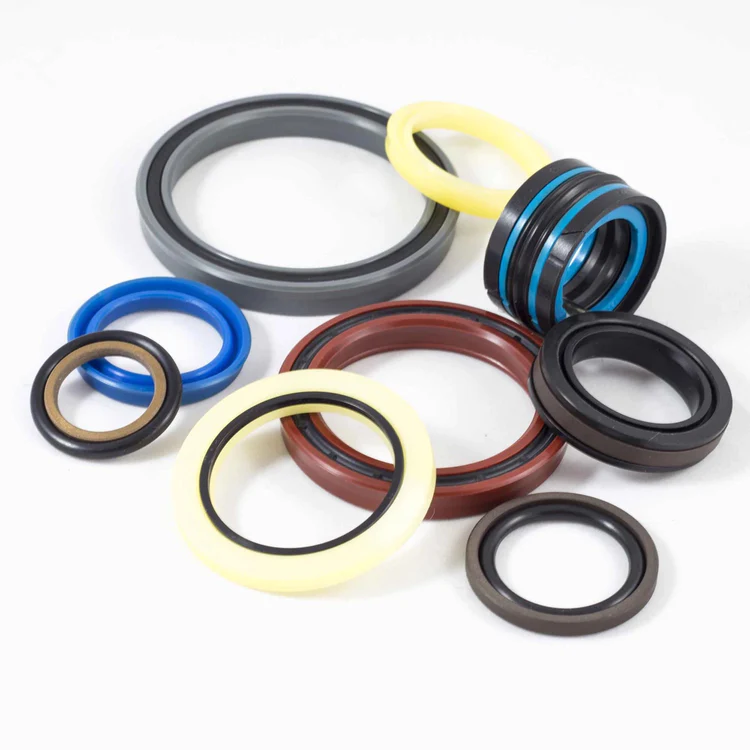
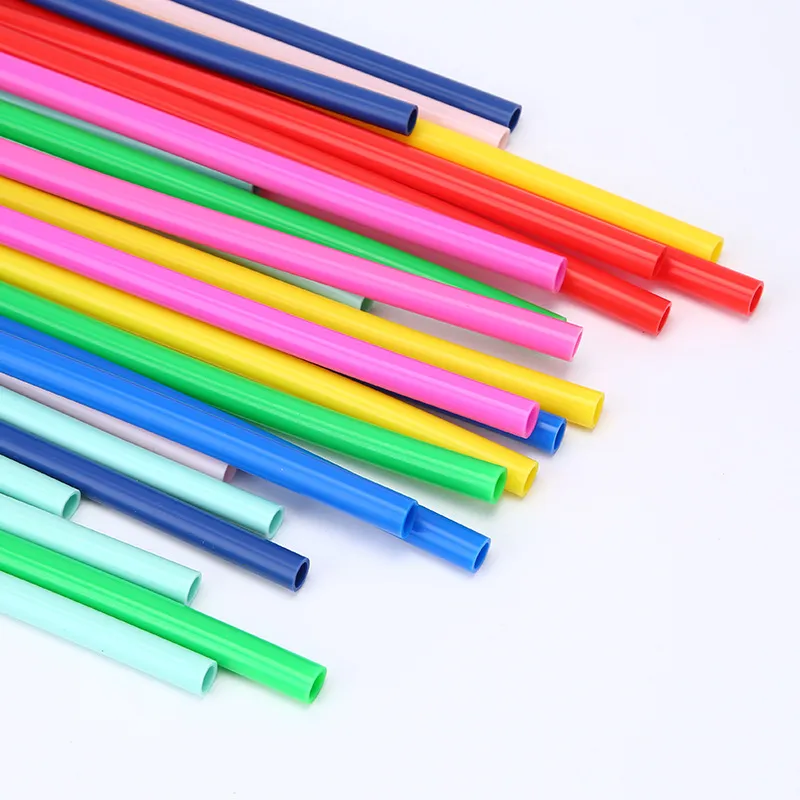
Flexibility: Silicone rubber is a flexible material that can be easily extruded into a variety of shapes and sizes. This flexibility makes it ideal for use in applications that require a high degree of flexibility and elasticity.
Durability: Silicone rubber is a highly durable material that is resistant to wear and tear, making it ideal for use in harsh environments. It can also withstand exposure to chemicals and UV radiation without degrading.
Temperature resistance: Silicone rubber is capable of withstanding extreme temperatures, both high and low, without losing its physical properties. This makes it an excellent material for use in applications that require exposure to extreme temperatures.
Weather resistance: Silicone rubber is also resistant to weather conditions such as rain, wind, and sunlight. This makes it an ideal material for outdoor applications that require long-term exposure to weather conditions.
Electrical insulation: Silicone rubber is an excellent electrical insulator, making it ideal for use in electrical applications where insulation is required.
Non-toxic and hypoallergenic: Silicone rubber is a non-toxic and hypoallergenic material that is safe for use in medical and food-related applications.
Low compression set: Silicone rubber has a low compression set, meaning that it can withstand repeated compression and retain its original shape, making it an excellent choice for sealing applications.
Applications of Extruded Silicone Rubber Strips And Gaskets
Extruded silicone rubber strips and gaskets are used in a wide range of industries and applications, including:
Automotive industry: Extruded silicone rubber gaskets and seals are used in engines, transmissions, and other critical components to prevent leaks and ensure proper functioning. They are also used in door seals, window seals, and other areas to provide a watertight and airtight seal.
Aerospace industry: Silicone rubber strips and gaskets are used in aerospace applications such as sealing doors, windows, and access panels. They are also used in vibration isolation systems and as thermal barriers in high-temperature environments.
Food processing industry: Silicone rubber strips and gaskets are used in food processing equipment such as ovens, mixers, and conveyors to provide a non-toxic and non-contaminating seal. They are also used in seals for food storage containers and as gaskets for food processing machinery.
Medical industry: Extruded silicone rubber gaskets and seals are used in medical devices such as surgical instruments, catheters, and implants. They are also used in medical equipment such as pumps, valves, and connectors.
Electronics industry: Silicone rubber strips and gaskets are used in electronics applications such as sealing and insulating electronic components, protecting them from moisture and other contaminants.
Construction industry: Extruded silicone rubber gaskets and seals are used in the construction industry to provide a watertight and airtight seal in windows, doors, and other areas.
Factors to Consider When Selecting Extruded Silicone Rubber Strips And Gaskets
When selecting extruded silicone rubber strips and gaskets, there are several factors that should be considered to ensure that the material meets the specific requirements of the application. Some of the most important factors to consider include:
(1) Temperature range: It is important to select a silicone rubber material that can withstand the temperature range of the application. High-temperature applications may require materials that can withstand temperatures up to 500°F or higher, while low-temperature applications may require materials that can withstand temperatures as low as -100°F.
(2) Chemical resistance: Silicone rubber is generally resistant to many chemicals, but the specific chemical resistance of the material should be considered when selecting a material for a specific application. Exposure to certain chemicals can cause the material to swell or degrade, which can affect its performance and durability.
(3) Compression set: The compression set is a measure of how much a material will deform under compression and how well it will return to its original shape after the compression is released. A low compression set is important for applications where the material will be compressed and released repeatedly, as it ensures that the material will maintain its seal over time.
(4) Physical properties: The physical properties of the silicone rubber material, such as its tensile strength, tear strength, and elongation, should be considered to ensure that the material can withstand the specific demands of the application.
(5) Environmental factors: The environmental factors of the application, such as exposure to sunlight, ozone, and moisture, should also be considered when selecting a silicone rubber material. Exposure to these factors can cause the material to degrade over time and affect its performance and durability.
(6) Regulatory compliance: Depending on the application, regulatory compliance may also be a factor to consider when selecting a silicone rubber material. Materials used in food and medical applications, for example, may need to meet specific regulatory requirements.
With the proper material and design, manufacturers can ensure their extruded silicone rubber strips and gaskets will stand up to anything; from vigorous environmental elements to challenging chemical components – all for optimal performance with durability that lasts.
As a silicone rubber manufacturer experts in silicone rubber seals manufacturing, our silicone rubber seals can endure tough working condition. If you are planing silicone rubber seals project, let us help you.