For several decades, silicone has been a mainstay in product development and manufacturing due to its many applications and sturdiness. Silicone, widely recognized for its toughness, pliability, and capacity to withstand high temperatures, serves as a necessity to many businesses, ranging from medical devices to kitchenware. Its silicon-oxygen backbone, which is decorated with organic groups and lends itself to an assortment of programs, is the foundation of its unique characteristics.
Liquid silicone rubber, or LSR, is a silicone material that has become unique in the industry and is becoming more and more well-liked. LSR is preferable to its solid counterparts in terms of processing and performance characteristics, which makes it perfect for producing complex and precise silicone parts. Its extensive use in a wide range of industries, particularly goods for consumers, automotive, healthcare, and aerospace, is a consequence of its resilience to adverse environments without compromising structural integrity.
This blog discusses the factors that have led to a developing inclination towards LSR as opposed to other silicone varieties and substitute materials. We will examine its special qualities, a broad spectrum of uses, as well as the advantages it provides—not just in terms of product performance but also in terms of sustainable production and the environment. Understanding why Liquid Silicone Rubber is the best option for silicone parts delivers valuable insights into how material science continues to advance and how it impacts daily life and technology.
Understanding Liquid Silicone Rubber (LSR)
Platinum-cured silicone in two components with high purity is identified as Liquid Silicone Rubber (LSR). It differentiates on account of its liquid state, which makes processing and molding straightforward. LSR is made up of a base polymer, a catalyst based on platinum, and other improvements that improve its physical properties. This mixture produces a material that is extraordinarily malleable, heat-resistant, and durable.
Comparison of LSR with Solid Silicone Rubber (SSR)
Solid Silicone Rubber (SSR) and Lithium Silicone Rubber (LSR) are both silicon derivatives, although they are processed and exist in various chemical states. SSR normally comes in a millable form which requires to be processed using conventional rubber methods like compression molding. However, since LSR is liquid, it may be injected into molds, enabling the creation of more complex and accurate part designs. Because LSR curing takes considerably less time than SSR, production cycles are shortened. Furthermore, compared to SSR, LSR often exhibits superior chemical resistance and thermal stability.
The Manufacturing Process of LSR
An innovative injection molding technique is used in the production of LSR. Up until shortly before the molding process, the two components of LSR—the catalyst and the basic silicone—are stored apart. After that, they are precisely combined and put into a mold that has been heated. The curing process is started by heat, which causes the material to solidify into the required shape. This method permits the creation of dependable, high-quality parts in huge numbers.
Advantages of LSR in Terms of Durability and Flexibility
LSR’s remarkable durability is one of its best qualities. It is capable of handling temperatures ranging from -55 to 300°C without losing its characteristics, which makes it suitable in harsh settings. Because of its unmatched flexibility, it can be utilized in situations where great elongation and flexibility are necessary without sacrificing strength. LSR is excellent for outdoor and harsh chemical applications because it doesn’t deteriorate when subjected to harsh chemicals or UV light. LSR is the best option for a wide range of products, from big automobile parts to microscopic medical devices, owing to its inherent flexibility and durability.
Key Properties of Liquid Silicone Rubber
• Thermal Stability and Heat Resistance
Liquid silicone rubber’s (LSR) extraordinary heat resistance is one of its most notable features. The temperature range that LSR can tolerate without degrading is -55°C to +300°C. Because of its remarkable thermal stability, it is the perfect material for applications that are subjected to high temperatures, such as cookware and under-the-hood car components. LSR, in contrast to many other materials, maintains its mechanical and flexible qualities even after having been subjected to high temperatures for a prolonged period of time.
• Chemical Resistance and Biocompatibility
Because of its remarkable chemical resistance, LSR can withstand a variety of substances, such as acids, alkalis, and oils. This characteristic can be particularly helpful in manufacturing facilities, where personnel frequently come into contact with harmful chemicals. Furthermore, a major contributing factor to LSR’s extensive application in the medical industry is its biocompatibility. It can be used in surgical devices, medical implants, and other healthcare applications since it is non-toxic, does not encourage the growth of organisms, and does not trigger allergic reactions.
• Electrical Insulation Properties
An exceptional electrical insulator is LSR. This property is essential for preventing electrical currents from flowing down undesirable routes during the production of electronic components. LSR is a recommended material for insulating cables and wires because of its thermal stability and insulating properties, particularly in environments with elevated temperatures.
• Optical Clarity and Colorability
The optical clarity of LSR is a further distinguishing trait. It may be rendered transparent, which is beneficial for lenses and other optical purposes. Moreover, LSR’s physical qualities can be retained while providing a broad spectrum of colors through easy pigmentation. Because of its colorability, it is capable of being used in more consumer goods where utility is not as vital as appearance.
• Elongation and Tear Strength
The elongation and tear strength of LSR have significance for applications that need longevity and flexibility. Its capacity to extend substantially without rupturing makes it indispensable for items such as gaskets, seals, and other flexible components. Due to their high tear strength, these products are guaranteed to remain trustworthy and permanent even under mechanical stress.
Overall, Liquid Silicone Rubber is a highly flexible and sought-after material across a variety of industries owing to its unique mix of heat resistance, chemical resistance, electrical insulation, optical clarity, and mechanical strength.
Applications of Liquid Silicone Rubber in Various Industries
• Medical and Healthcare: Implants and Medical Devices
Use in Implants: Because LSR is biocompatible, it is perfect for long-term implanted devices, like joint replacements and heart valve replacements. One important characteristic is that the substance stays stable in the human body without causing any negative effects.
Medical Devices: It is frequently found in medical instruments, surgical tubing, and respiratory masks. The widespread use of LSR in delicate medical applications can be attributed to its flexibility and its ability to be sterilized without deterioration.
• Automotive: Gaskets, Seals, and Connectors
Gaskets & Seals: LSR is perfect for engine gaskets, oil seals, and hoses because of its heat and chemical resistance, which guarantees durability under difficult conditions at work.
Electrical Connectors: The production of trustworthy and secure electrical connectors and vehicle insulation relies on LSR’s electrical insulation qualities.
• Consumer Products: Kitchenware, Electronics, and Wearables
Kitchenware: LSR is a well-liked substance for cookware such as baking molds, spatulas, and food storage containers because of its heat resistance and non-toxicity.
Electronics and Wearables: Protective cases, keypads, and wearable devices that need to be pleasant to use and resilient to wear and tear are excellent solutions for LSR’s flexibility and durability.
• Aerospace: Insulation and Damping Solutions
Insulation: LSR is used in aerospace for protective components and wiring insulation because of its insulating qualities along with its ability to tolerate high temperatures.
Damping Solutions: Their capacity to dampen vibrations makes it crucial for lowering noise levels and safeguarding delicate components of aircraft from mechanical stress.
Each of these case studies exemplifies the diverse applications of Liquid Silicone Rubber, showcasing its indispensable role in advancing technology and improving the quality of products across various industries.
The Advantages of Liquid Silicone Rubber Over Other Materials
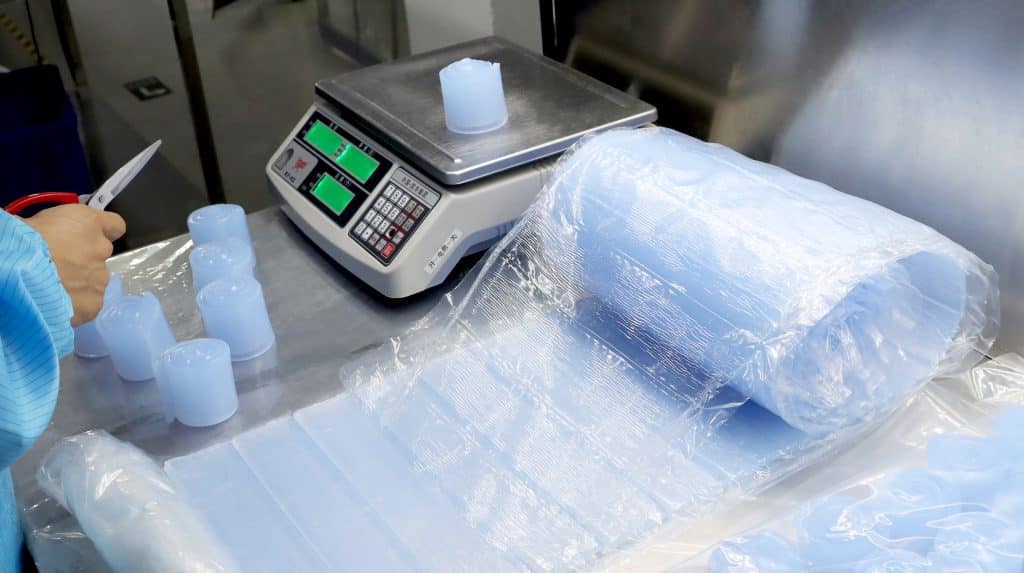
• Thermal Resistance
When it comes to heat resistance, LSR performs better than a lot of thermoplastics and other rubbers, maintaining its qualities in very high temperatures where others would break down.
• Chemical Stability
LSR is more resilient in abrasion settings due to its greater resistance to chemicals, oils, and UV radiation than many thermoplastics and rubbers.
• Suppleness and Strength
LSR strikes a balance between improved tensile and tear strength and the suppleness of conventional rubbers, which is difficult to accomplish with thermoplastics or other rubbers.
• Inexpensive and Long-Term Sturdiness
Lower Lifecycle Costs: Although LSR may initially cost more than some materials, over time it will save money because fewer substitutes will be needed due to its long lifespan.
• Minimal Maintenance
Being resistant to deterioration indicates that it requires less maintenance, which is important in sectors like aerospace and automotive.
• Fast Curing and Processing
LSR may be produced in large quantities without compromising quality as a result of its short curing time and compatibility with precision injection molding.
•Flexibility
LSR offers an extensive number of design options because it can be molded into elaborate, complex shapes that would be difficult or impossible to create with other materials.
• Customization of Color and Characteristics
LSR is easily pigmentable and can be modified with additives to meet specific application needs, such as improved conductivity or harderness.
• Potential for Recycling and Eco-Friendliness
Reduced Energy Consumption: Compared to thermoplastics, LSR processing typically consumes less energy, providing a lower carbon imprint.
• Recycling and Waste Reduction Silicone materials are becoming more environmentally friendly thanks to advancements in recycling technologies, such as LSR. Industrial waste can be decreased by grinding and reusing cured LSR in new compounds.
With its outstanding heat and chemical resistance, in addition to its efficient processing, Liquid Silicone Rubber is a better material choice for many applications. Its unique combination of performance, economy, and environmental factors sets it apart from different substances used in contemporary manufacturing processes.
Future Trends and Developments in Liquid Silicone Rubber
Liquid Silicone Rubber (LSR) stands out in the material science landscape for its exceptional properties and versatility. Its unparalleled heat resistance, flexibility, and durability make it superior to many traditional materials like thermoplastics and other rubbers. Widely used in diverse industries from medical to automotive and consumer goods, LSR’s adaptability is evident in its vast range of applications. While there are challenges in processing and manufacturing, ongoing technological advancements are continually addressing these issues. The future of LSR is particularly promising, with emerging technologies enhancing its properties and expanding its applications into new realms like biomedical devices and sustainable energy solutions. As we advance, LSR’s role in driving innovation and contributing to sustainable manufacturing practices underscores its significance in the evolving world of material science.