Viton® O-Rings, a term frequently employed in industrial and technical fields, refer to a specific form of sealing ring produced by Viton®, a fluoroelastomer. These O-rings are well-known for their excellent chemical resistance, high-temperature stability, and durability. This blog will review the intricate details of Viton® O-rings, including their composition, qualities, applications, advantages, and comparison to other types of O-rings.
What Are Properties of Viton® O-Rings?
Viton® O-rings are renowned for their superior characteristics, which make them vital in demanding industrial applications. These fluoroelastomer (FKM) seals are well regarded for their outstanding resistance to heat, chemicals, fuels, oils, and lubricants. This robustness assures that Viton® O-rings maintain their integrity even at extreme temperatures ranging from -15°C to 204°C (-5°F to 400°F), making them suited for both high and low-temperature use.
Furthermore, Viton® O-rings have excellent strength and long-term performance, as seen by their strong resistance to compression set, which allows them to maintain their sealing effectiveness over time. Their resistance to ozone and weathering improves their reliability in outdoor and harsh environmental situations, ensuring unchanged operation in avariousmanufacturing settings.
Furthermore, Viton® O-rings have exceptional mechanical characteristics such as tensile strength, tear resistance, and elongation. These characteristics make them ideal for applications demanding high sealing performance and lifespan, such as the automobile, aerospace, chemical processing, and oil and gas industries. Overall, Viton® O-rings are considered a reliable sealing solution, known for their chemical resistance and operational versatility in an extensive variety of industrial applications.
The Importance of O-Rings in Industry
O-rings are circular gaskets that sit in a groove and compress during assembly between two or more pieces, producing a seal at the interface. They prevent liquids or gasses from passing through the mechanical assembly, ensuring its integrity.
Common Materials Used in O-Rings
O-rings are critical components in an extensive variety of mechanical systems, and their performance is heavily dependent on the materials from which they are produced. Each material has unique characteristics that are adapted to certain purposes. Here’s an overview of various typical materials used in O-rings, emphasizing their performance characteristics, traits, and distinguishing features.
Nitrile Rubber (NBR) is an increasingly common material for O-rings due to its exceptional resistance to oils, fuels, and hydraulic fluids. It is widely recognized for its ability to endure extreme temperatures ranging from -40°C to 100°C (-40°F to 212°F). Nitrile O-rings are also resistant to abrasion and have a high degree of mechanical integrity, making them ideal for automotive, industrial, and aerospace applications where petroleum-based fluids are commonly used. Their cost-effectiveness and versatility make NBR a popular choice for many sealing needs.
Fluoroelastomer (FKM), additionally referred to as Viton®, stands out for its excellent resilience to harsh temperatures ranging from -15°C to 204°C (-5°F to 400°F). FKM O-rings are particularly resistant to chemicals, fuels, oils, and ozone, making them perfect for use in severe environments like chemical processing and aircraft. Their resistance to temperatures deterioration and compression set ensure long-term performance and trustworthiness, especially during severe situations.
Silicone Rubber is another common material used in O-rings due to its powerful temperature stability, which can resist temperatures that vary between -60°C to 200°C (-76°F to 392°F). Silicone O-rings are exceptionally adaptable, even at high temperatures, and highly resistant to aging, ozone, and weathering.
Although they may not be as resistant to chemicals as NBR or FKM, their ability to maintain flexibility and sealing qualities in a variety of situations makes them ideal for use in medical devices, food processing, and automotive industries.
EPDM (Ethylene Propylene Diene Monomer) O-rings are distinguished by their outstanding resistance to water, steam, and diverse weather conditions, making them an ideal choice for applications that need outside exposure. They operate well in temperatures ranging from -40°C to 150°C (-40°F to 302°F) and are noted for their high ozone and UV acceptance. EPDM O-rings are used extensively in the automotive, HVAC, and plumbing industries due to their high durability and durability to environmental degradation.
Polyurethane (AU) O-rings have outstanding resistance to wear and tensile strength, making them ideal for use in abrasion and high-pressure settings. They can withstand temperatures that vary between -30°C to 80°C (-22°F to 176°F) and are noted for their high resilience to tearing and impact. Polyurethane O-rings are widely employed in hydraulic and pneumatic systems, where their toughness and durability are extremely beneficial.
Advantages of Viton® O-Rings
Viton® O-rings, crafted from fluoroelastomer (FKM), are highly esteemed in various industries for their superior performance and reliability. One of the primary advantages of Viton® O-rings is their exceptional resistance to high temperatures. They maintain their sealing integrity in extreme thermal environments, typically ranging from -15°C to 204°C (-5°F to 400°F). This thermal stability makes them ideal for applications in aerospace, automotive, and chemical processing, where temperature fluctuations and high heat are common.
In addition to their thermal resilience, Viton® O-rings are renowned for their outstanding chemical resistance. They offer excellent protection against a broad spectrum of chemicals, including oils, fuels, acids, and solvents.
Viton® O-rings made from fluoroelastomer (FKM) are highly regarded in a variety of industries due to their outstanding performance and dependability. One of the most notable benefits of Viton® O-rings is their exceptional durability in high temperatures. They keep their sealing integrity in severe temperatures ranging from -15°C to 204°C (-5°F to 400°F). High thermal stability makes them perfect for applications like aerospace, automotive, and chemical processing, where fluctuations in temperature and high heat are typical.
In addition to its thermal robustness, Viton® O-rings are renowned for their exceptional chemical resistance. They provide excellent safeguards from a wide range of chemicals including oils, fuels, acids, and solvents.
Viton® O-rings’ excellent chemical resistance preserves their efficiency in difficult chemical conditions, making them important in industries such as petrochemical, pharmaceutical, and automotive.
Viton® O-rings are also exceptionally resistant to ozone, weathering, and aging. Unlike many other materials that degrade when exposed to outside influences, Viton® O-rings maintain their flexibility and sealing efficacy even when exposed to ozone, UV radiation, and extreme weather. This feature increases their longevity and trustworthiness, reducing the need for frequent replacements and maintenance.
Viton® O-rings have another key advantage: they are resilient to compression sets. This feature ensures that the O-rings retain their shape and sealing qualities over time, even when continually compressed. This resistance to compression set adds to the overall endurance and effectiveness of Viton® O-rings in maintaining a secure seal in dynamic and static situations.
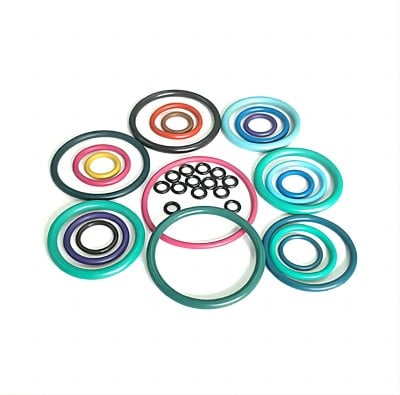
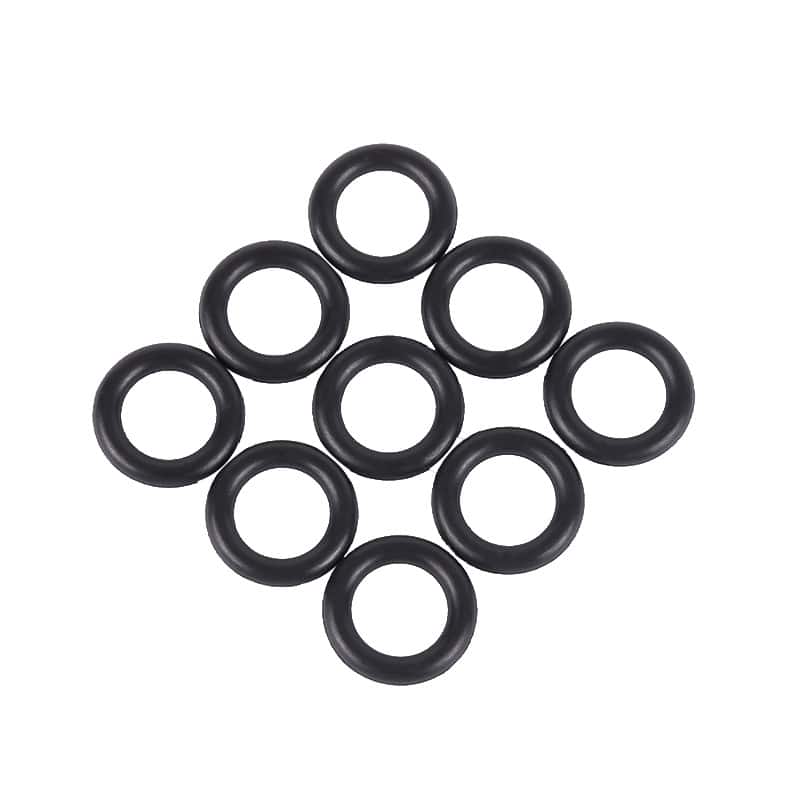
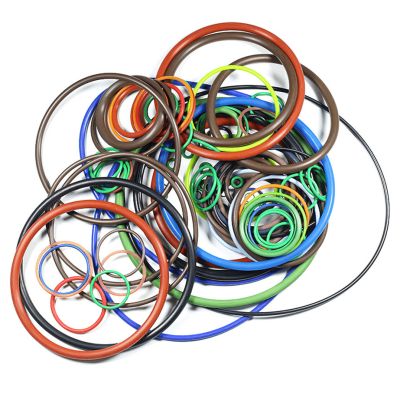
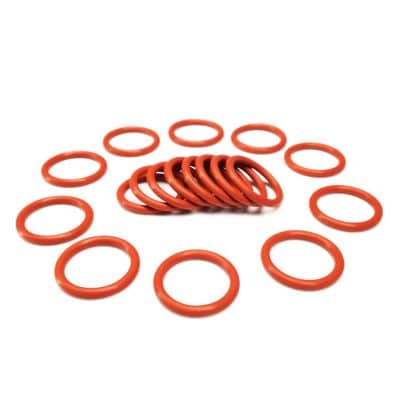
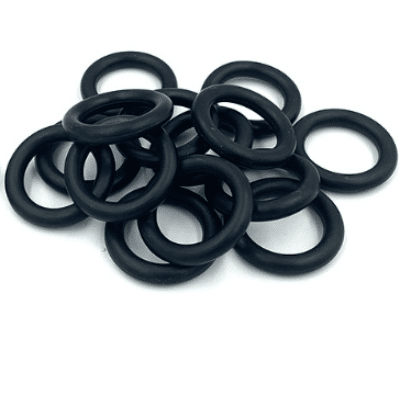
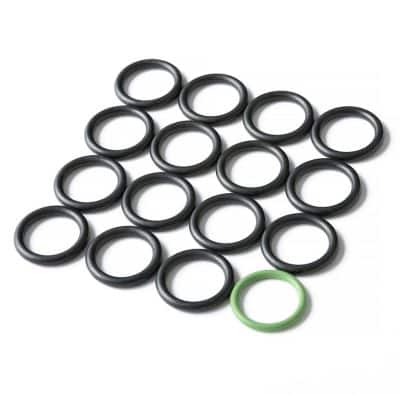
Applications of Viton® O-Rings
Viton® O-rings are well-known for their flexibility and durability, making them suited for a wide range of demanding applications across multiple industries. Viton® O-rings are commonly used in aircraft applications such as engines, fuel systems, and hydraulic systems. Their ability to withstand severe temperatures, as well as harsh fuels and chemicals, is crucial to preserving aerospace component reliability and safety.
Viton® O-rings are essential in the automotive industry for maintaining engine and transmission system performance and lifetime. They are widely employed in fuel injectors, turbochargers, and oil seals, where their resistance to high temperatures and fuels aids in preserving peak performance and lowering the chance of leaks and failures. Their longevity in difficult operating conditions adds greatly to the overall reliability of automotive systems.
Viton® O-rings’ outstanding qualities are extremely beneficial in the chemical processing industry. These seals are used in a variety of applications, including pumps, valves, and mixers, where they are exposed to harsh chemicals, acids, and solvents. Viton® O-rings’ chemical resistance ensures that they retain sealing integrity and operating efficiency even in difficult and corrosive conditions.
Viton® O-rings are essential in the automotive industry for maintaining engine and transmission system performance and lifetime. They are widely employed in fuel injectors, turbochargers, and oil seals, where their resistance to high temperatures and fuels aids in preserving peak performance and lowering the chance of leaks and failures. Their longevity in difficult operating conditions adds greatly to the overall reliability of automotive systems.
Viton® O-rings additionally serve in medical and pharmaceutical applications as sealing solutions. Viton® O-rings provide the required durability and resistance in devices and equipment that require cleanliness and sterilization. Their ability to work even after repeated exposure to cleaning agents and sterilizing processes makes them excellent for use in medical devices and pharmaceutical manufacturing equipment.
Comparing Viton® O-Rings to Other O-Rings
When comparing Viton® O-rings to other types of O-rings, many reasons dimensions—such as temperature resistance, chemical resistance, environmental stability, and cost-effectiveness—showcase their unique benefits and limits.
• Temperature Resistance
Viton® O-rings are popular for their extreme temperature tolerance, operating efficiently in temperatures ranging from -15°C to 204°C (-5°F to 400°F). This contrasts with materials like Nitrile Rubber (NBR), which can resist temperatures ranging from -40°C to 100°C (-40°F to 212°F). While NBR is successful in a wide range of automotive and industrial applications, Viton® O-rings perform better in high-temperature environments, making them outstanding for aerospace and high-performance automotive applications where extreme thermal conditions are prevalent.
• Chemical Resistance
Viton® O-rings are exceptionally resistant to a variety of chemicals, including oils, fuels, acids, and solvents. This level of chemical resistance is higher than that of many other materials. For example, NBR O-rings are impervious to oils and fuels but less effective against some acids and solvents. Fluorosilicone O-rings, while resistant to fuels and oils, are not as chemically resistant as Viton® in harsher circumstances. Thus, Viton® O-rings are preferred in industries such as chemical processing and oil & gas, where exposure to strong chemicals is a concern.
• Environmental Stability
Viton® O-rings are exceptionally resistant to ozone, UV radiation, and weathering. This environmental stability is preferable to materials like EPDM (Ethylene Propylene Diene Monomer), which, while water and weather-resistant, may lack Viton®’s UV and ozone safeguarding. Viton® O-rings’ exceptional durability enables long-lasting performance in outdoor and exposed situations, making them ideal for use in challenging locations.
• Cost-Effectiveness
While Viton® O-rings provide outstanding temperature and chemical resistance, they are often more expensive than materials such as NBR and EPDM. NBR O-rings, for instance, are more affordable for regular applications in which severe temperatures and chemical exposure are not a key concern. As a result, selecting between Viton® and other O-ring materials often involves balancing requirements for performance with financial limitations.
Viton® O-rings are an essential component in an extensive variety of industrial applications, providing exceptional chemical resistance, temperature tolerance, and durability. Their unique characteristics make them indispensable in tough circumstances ranging from the automotive and aerospace industries to chemical processing and more. Understanding the benefits and selecting the correct Viton® O-ring can help devices and networks run more effectively, safely, and for longer. As industries grow, high-performance sealing solutions such as Viton® O-rings will continue to play an important role in driving technical and operational breakthroughs.