Silicone extrusion is a manufacturing process in which a continuous length of silicone material is created by pushing it through a shaped die. This process can be used to create products such as tubing, seals, and gaskets in a variety of sizes and shapes.
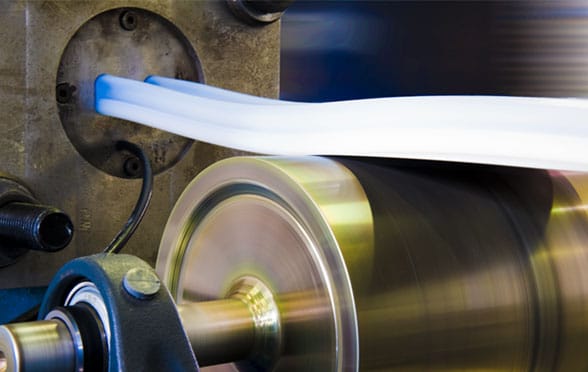
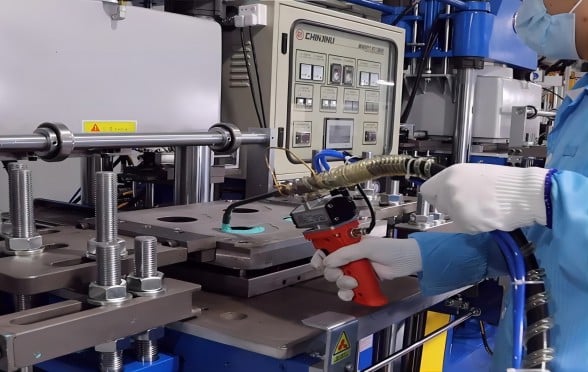
Silicone injection molding, on the other hand, is a manufacturing process in which liquid silicone material is injected into a mold cavity under high pressure, where it solidifies and takes the shape of the mold. This process can be used to create complex shapes with high precision and accuracy, such as phone cases, medical devices, and automotive parts.
Importance of Choosing The Right Manufacturing Process for Your Product
Selecting the right manufacturing process is paramount to a product’s success. When appropriately applied, this decision can shape factors like performance quality, cost-effectiveness, and marketability – all of which are instrumental in gaining consumer interest and trust. However, an incorrect selection could lead to products with inadequate durability or not meeting required tolerances which ultimately translates into poor reviews from customers and decreased sales opportunities. The opposite outcome is also possible: when chosen correctly businesses will reap the rewards of high customer satisfaction ratings as well as increased sales numbers due to more competitive pricing offering consumers greater value for their money. The manufacturing process may have a considerable influence on the product’s environmental footprint, longevity, and regulatory adherence. Companies need to consider these factors when selecting their production methods to ensure they’re making choices that reflect company values while adhering to industry regulations.
Silicone Extrusion
Silicone extrusion is a manufacturing process that involves pushing a continuous length of silicone material through a shaped die to create a product with a constant cross-section. The silicone material is typically heated and then forced through the die using a ram or screw extruder. The die is designed to produce the desired shape, and the silicone material is cooled as it exits the die to maintain the shape.
Silicone extrusion can be used to create products such as tubing, seals, gaskets, and profiles in various sizes and shapes. This process offers several advantages, including cost-effectiveness for high-volume production, versatility in product design, and the ability to create continuous lengths of silicone products. However, the precision of the product dimensions may be limited, and the tooling costs for complex designs can be high.
Silicone extrusion is commonly used in industries such as medical devices, automotive, aerospace, and construction. It’s a popular choice for creating products that require flexibility, resistance to extreme temperatures, and chemical resistance.
Advantages of Silicone Extrusion
Ability to create continuous lengths of silicone products: The extrusion process allows for the creation of products with a consistent cross-section and the ability to produce them in a continuous length, which can be cut to size as needed. This makes silicone extrusion an ideal process for creating long tubing or other products that require uniformity in size and shape.
Cost-effectiveness for high-volume production: Extrusion can be a cost-effective process for producing large volumes of products due to the ability to create multiple identical shapes simultaneously. This can reduce labor costs and lead times while increasing overall productivity.
Versatility in product design: Extrusion can be used to create a wide range of shapes and sizes with various profiles and cross-sections. This makes it a versatile process that can be used to create products with different functions, including seals, gaskets, and profiles.
Consistent quality: Silicone extrusion allows for tight control over the manufacturing process, ensuring consistent product quality with every run. This results in products that meet high standards of performance and reliability.
Limitations of Silicone Extrusion
While silicone extrusion has many advantages, there are also some limitations to consider when choosing this manufacturing process, including:
Limited precision of product dimensions: The precision of product dimensions may be limited by the design of the die used in the extrusion process. As a result, it may not be the best process for creating highly precise or complex parts that require tight tolerances.
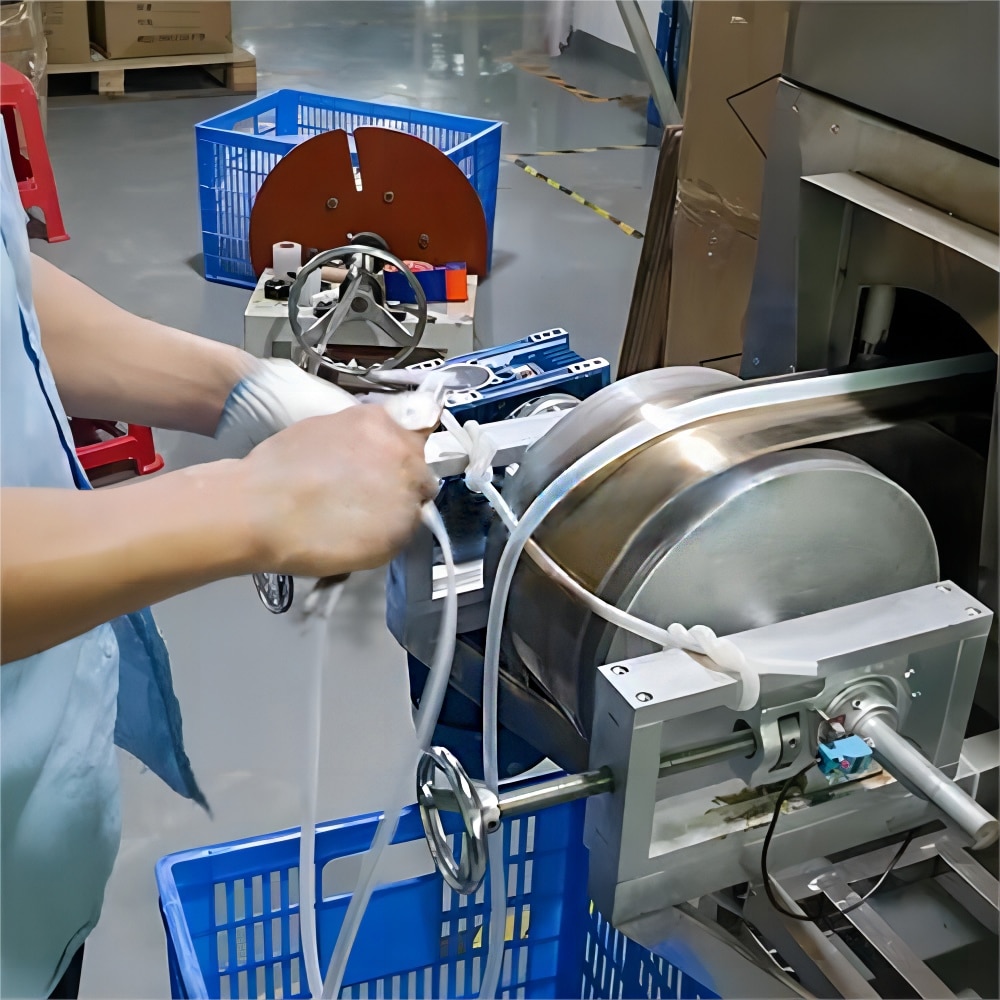
Limited material options: Silicone extrusion is limited to using silicone as the primary material. While silicone is versatile and has many applications, it may not be the best material for every product.
High tooling costs for complex designs: The cost of creating the dies used in the extrusion process can be high, especially for complex designs. This may make silicone extrusion less cost-effective for low-volume or custom production runs.
Limited design flexibility: While silicone extrusion is versatile in terms of creating different profiles and cross-sections, it may not be the best process for creating highly customized designs with unique shapes or features.
Silicone Injection Molding
Injection molding is a manufacturing process in which liquid silicone material is injected into a mold cavity under high pressure, where it solidifies and takes the shape of the mold. The process involves several stages, including material preparation, injection, packing, cooling, and ejection.
During the material preparation stage, the silicone material is mixed, heated, and loaded into the injection molding machine. The machine consists of two main components: the injection unit and the clamping unit. The injection unit is responsible for melting the silicone material and injecting it into the mold cavity, while the clamping unit holds the mold in place and applies pressure to keep it closed during the injection process.
Once the mold is closed, the silicone material is injected into the mold cavity under high pressure. The material fills the cavity and takes the shape of the mold. The packing stage then follows, where additional pressure is applied to the material to ensure it fills the mold cavity.
After packing, the mold is cooled to solidify the silicone material, and the ejection stage follows. The mold is opened, and the finished product is ejected from the machine. The product is then trimmed, inspected, and ready for use or further processing.
Injection molding is ideal for creating complex shapes with high precision and accuracy. It can be used to produce a wide range of products, including medical devices, automotive parts, and consumer goods. The process offers several advantages, including the ability to produce high-quality, consistent parts at a relatively fast rate, with minimal material waste.
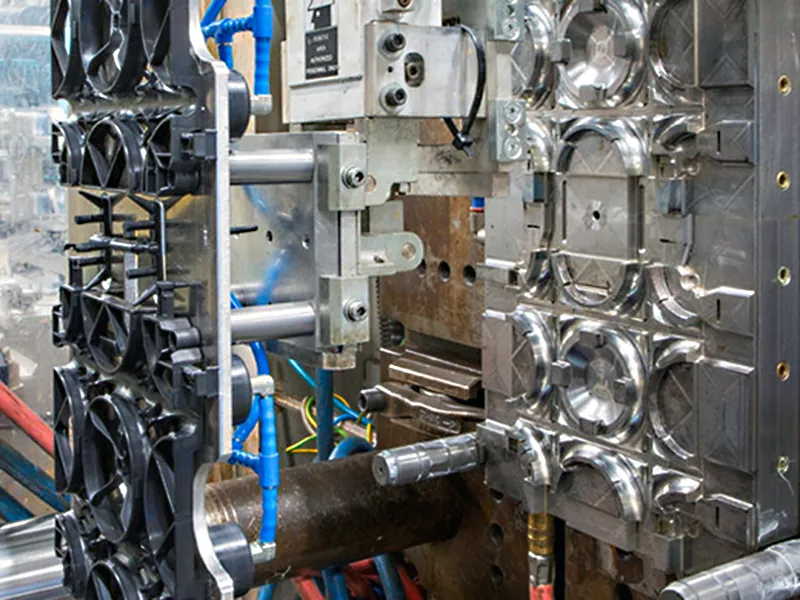
Advantages of Injection Molding
Injection molding offers several advantages as a manufacturing process, including:
(1) High precision and accuracy: Injection molding can produce complex shapes with high precision and accuracy, making it ideal for creating parts that require tight tolerances and intricate designs.
(2) High efficiency and productivity: Injection molding is a fast and efficient process that can produce a high volume of parts in a short amount of time. The process can be automated, further increasing productivity.
(3) Material flexibility: Injection molding can be used with a wide range of materials, including thermoplastics, thermosets, and liquid silicone rubber. This allows for a high degree of flexibility in material selection, making it easier to find the right material for each product.
(4) Reduced waste: Injection molding generates less waste than other manufacturing processes, as any excess material can be reused. This makes it a more sustainable option for production.
Reduced labor costs: Injection molding can be a cost-effective option for high-volume production runs, as it requires less labor compared to other processes.
Limitations of Injection Molding
While injection molding has many advantages, there are also some limitations to consider when choosing this manufacturing process, including:
High initial tooling costs: Injection molding requires the creation of a mold or tooling, which can be expensive, especially for complex or large parts. This can make injection molding a less viable option for low-volume production runs.
Limited design flexibility: Injection molding is best suited for creating parts with uniform wall thickness and simple geometries. Complex shapes or parts with varying wall thicknesses may be difficult or impossible to produce with injection molding.
Long lead times: The process of creating a mold for injection molding can take several weeks or even months, which can add to the overall lead time for the production of the parts.
Material limitations: While injection molding can be used with a wide range of materials, certain materials may not be suitable for the process. For example, some materials may require high processing temperatures that can damage the mold or create other issues.
Part size limitations: Injection molding may not be suitable for creating large parts or products, as the size of the mold is limited by the size of the injection molding machine.
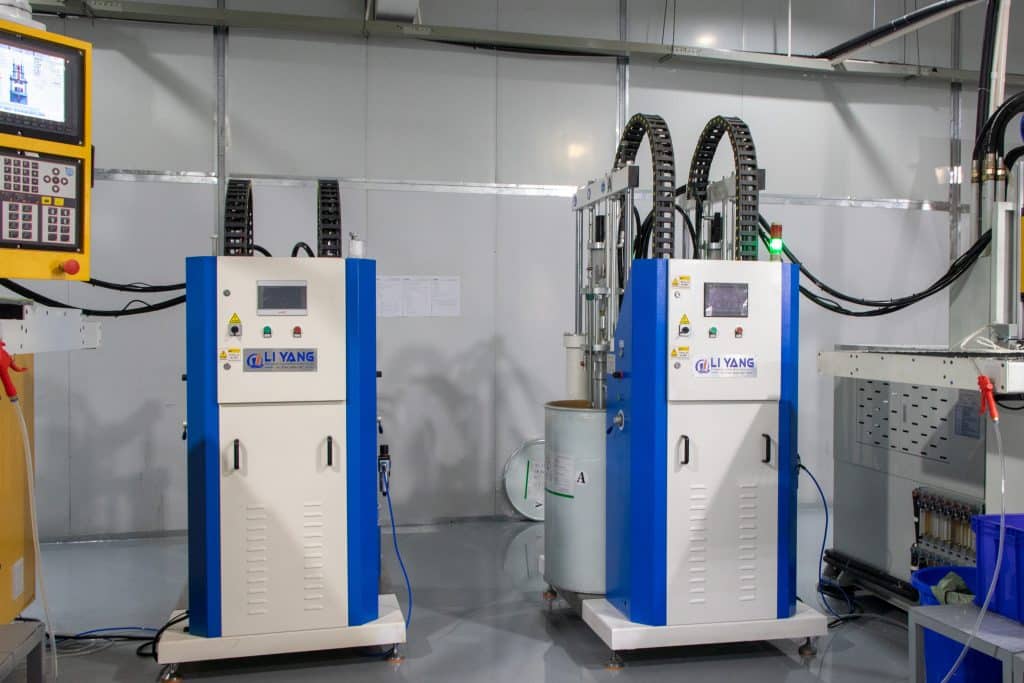
Factors to Consider When Choosing A Process
When deciding between silicone extrusion and injection molding for a particular product, there are several factors to consider, including:
Product design: The complexity and geometry of the product design will impact which manufacturing process is more suitable. Silicone extrusion is best suited for creating parts with consistent cross-sections, while injection molding can produce more complex shapes with high precision and accuracy.
Production volume: The volume of parts needed will impact the cost-effectiveness of each manufacturing process. Silicone extrusion is better suited for low to medium-volume production, while injection molding is more cost-effective for high-volume runs.
Material requirements: The type of material needed for the product will also impact which process is more suitable. While both processes can work with silicone materials, injection molding can work with a wider range of materials, including thermoplastics, thermosets, and liquid silicone rubber.
Lead time: The lead time for each process is also an important factor to consider. Silicone extrusion has a shorter lead time since it does not require the creation of a mold, while injection molding can take several weeks or months to produce the mold.
Cost: The overall cost of each process, including tooling costs, material costs, and labor costs, should be considered when choosing a manufacturing process.
Ultimately, the decision between silicone extrusion and injection molding will depend on the specific requirements of the product and production process. Careful consideration of each factor can help ensure that the chosen process is the most efficient, cost-effective, and suitable option for the product.