Our electronic gadgets are more than simply tools in the digital age we live in; they are integral to our everyday routines. These devices, which range from laptops and tablets to smartphones and tablets, store our sensitive personal and professional information as well as priceless memories. It’s imperative to protect these priceless gadgets, which is why silicone protective cases are useful.
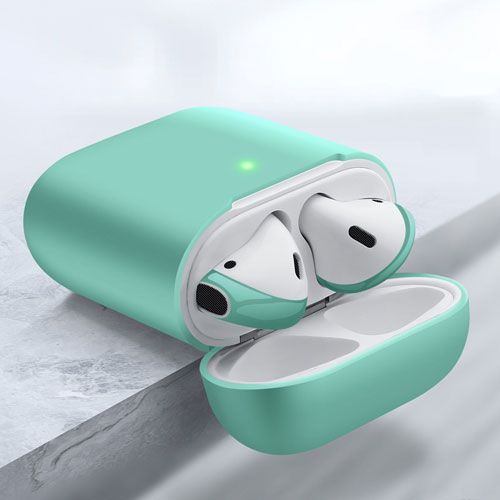
A cheap and practical method of protecting gadgets from normal use-related wear and tear is to use protective cases. They offer a shield against dings, falls, and other possible harm, providing that your gadget remains in perfect shape for an extended period. But not every protective case is made equal. Customizing a silicone protective case has several unique benefits over regular cases.
Specifically designed to fit your device, custom silicone protective cases guarantee that all buttons, ports, and features are readily accessible. Additionally, they enable customized designs, letting you showcase your personal taste or brand identity. Furthermore, silicone is a perfect material for long-lasting, high-quality protective covers because of its inherent qualities, which include flexibility, durability, and resistance to extreme temperatures.
We’ll go into how to make a personalized silicone protective case in this blog, examine the advantages of customization, and emphasize why NEWTOP is your reliable manufacturing partner for silicone products.
Why Choose Silicone Rubber?
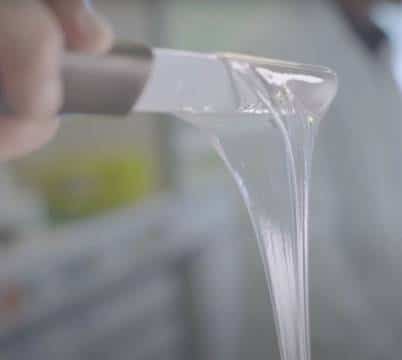
(1) Properties of Silicone
Silicone is a material that can be used for numerous applications and is particularly useful in protective cases because of its special qualities. These are a few of silicone’s main characteristics:
Durability: Because silicone is so immune to abrasion and wear and tear, protective cases composed of it can endure regular use without suffering damage.
Flexibility: This material is extremely elastic, which enables it to comfortably fit around devices of different sizes and shapes while also absorbing impacts.
Temperature Resistance: Silicone retains its structural integrity even in extremely hot or cold temperatures. It is therefore perfect for usage in a variety of settings.
Water Resistance: Due to silicone’s natural resistance to water, an additional layer of defense against spills and splashes is provided.
Chemical Resistance: The case’s resistance to many different chemicals, such as oils and solvents, contributes to its ability to retain its functionality and appearance over time.
(2)Advantages of Silicone for Protective Cases
Due to its special qualities, silicone is the material of choice for making protective cases for electronic devices. Here are a few benefits:
Non-Toxicity: Silicone is safe to use in products that come into contact with food or skin because it is not a toxic material. This is particularly important for portable electronics like wearables.
Cleaning Ease: Silicone cases are straightforward to keep clean. They are safe to wash with soap and water to maintain their fresh appearance and hygiene.
Shock Absorption: Silicone’s flexibility and resilience enable it to effectively absorb shocks, offering superior protection against knocks and impacts.
Customizability: A great deal of customization can be performed because silicone is easily molded into a variety of shapes and designs. This makes possible the creation of cases that are both aesthetically beautiful and functional.
Comfort and Grip: The slightly tacky surface of silicone offers a good grip, lowering the possibility of unintentional falls. Its soft texture additionally guarantees a comfortable grip.
Knowing silicone’s benefits and qualities, it’s quickly readily apparent why protective case manufacturers love to use this substance so much. Its endurance, adaptability, and safety features guarantee that your gadget is well-protected while also letting you express your unique personality with custom designs.
What Are The Applications of Silicone Protective Cases?
Silicone casings are a flexible and popular choice for many kinds of gadgets. Their special qualities make them suitable for use in specialized industrial and medical equipment as well as everyday consumer electronics. The following are some important uses for silicone protective cases:
(1) Personal Electronics
Smartphone cases made of silicone offer superior defense against falls, scuffs, and normal wear and tear. They guarantee that ports and buttons stay accessible while maintaining the device’s security by offering a snug fit.
Tablets: Silicone cases for tablets provide an extra layer of cushioning to guard against knocks and unintentional drops. Additionally, they may have grips or stands for increased functionality.
Laptops: Silicone covers for laptops can provide heat resistance in addition to protection from scratches and bumps, which is particularly beneficial for devices that heat up swiftly.
(2)Wearable Devices
Smartwatches: Watch bands and covers made of silicone protect the gadget from dents, knocks, and moisture. They are available in a variety of hues and patterns and are quite comfy to wear.
Fitness Trackers: Silicone cases are a great addition to fitness trackers since they are used during physical activities. These cases ensure that the gadget stays safe and functional during exercises because of its durability and water resistance.
(3)Other Gadgets
Cameras: For both amateur and professional photographers, silicone protective cases for cameras provide shock absorption and weather protection.
Remote controls: Silicone covers provide a better grip while also safeguarding the device from spills and drops.
E-readers: E-reader silicone cases boost the device’s durability by shielding it from dings and knocks.
(4) Industrial and Medical Equipment
Specialized Applications: To shield delicate equipment from adverse environments, silicone protective cases are utilized in industrial and medical settings. To ensure a perfect fit and the best possible protection, these cases can be tailored to fit particular devices.
Medical Devices: Silicone covers shield equipment from damage and contamination in medical settings. They resist repeated cleanings and are simple to sterilize.
Industrial Tools: Silicone cases protect industrial tools and equipment from moisture, dust, and mechanical impacts, thereby extending their lifespan.
Silicone protective cases supply protection, customization, and improved functionality, making them a necessary addition to a variety of devices. Devices are kept safe, dependable, and long-lasting with silicone cases—whether for personal use or particular purposes.
Benefits of Silicone Protective Cases
There are many advantages to customizing a silicone protective cover for your device that regular cases just cannot compare to. The following are strong arguments in favor of choosing a personalized silicone protective cover:
(1) Ideal Fit
Accessibility: All ports, buttons, and features are easily reachable thanks to a custom silicone case that is made to fit your device specifically. The seamless use of the device is ensured by its precise fit, which prevents the need to remove the case to access any of its purposes.
Compatibility: Custom cases have been created to fit your device’s specific dimensions and shape, which is especially important for those with unusual setups or extra accessories.
(2) Customization Solution
Custom silicone cases allow you to personalize the design of your device to reflect your brand or personal style. You can create a case that expresses your individuality or brand identity by selecting from a large selection of hues, patterns, and textures.
Branding: Custom cases are an excellent instrument for marketing and brand recognition for businesses because they can incorporate logos and branding elements. Personalized cases make thoughtful business gifts or different promotional merchandise.
(3) Enhanced Defense
Enhanced Security: Enhanced protection against drops, scratches, and impacts is a feature of custom cases. Because of the customized fit, there is a lower chance of damage to your device given that the case absorbs shock more effectively.
Durability: Custom cases made of premium silicone provide enduring protection, guaranteeing that your device is kept safe over time. In particular, devices used in demanding environments need to be long-lasting.(4) Extra Features
Functional Enhancements: You can request custom silicone cases with features that are tailored to your needs. To increase your case’s functionality and versatility, you can, for instance, add grips, stands, or card holders.
Ergonomic Design: Customization allows ergonomic enhancements that make the device more comfortable to hold and operate, like increased grips or textured surfaces.
You can make sure that your gadget is well-protected and fits your needs by personalizing the silicone protective cover. It also looks wonderful. Custom silicone cases give unparalleled benefits in terms of fit, design, protection, and functionality, whether they are utilized for personal or professional purposes.
How to Create a Custom Silicone Protective Cover
To make sure the finished product fulfills your specific needs and expectations, there are a few essential steps involved in creating a custom silicone protective cover. Here is a thorough how-to guide:
Step 1: Identify the Specifications of Your Device
Accurately Measure the Device’s Dimensions: Start by precisely determining the length, width, height, and any distinct contours of your device.
Take Note of the Buttons, Ports, and Other Elements’ Positions: Make sure you record where all the buttons, ports, cameras, and other features that must stay accessible are located. This guarantees that your bespoke case will fit precisely and won’t interfere with any necessary operations.
Step 2: Select Your Style
Choose your hues, patterns, and textures: Select the overall design of your case. Select hues, patterns, and textures that go well with your aesthetic or brand identity.
Select Extra Design Components: If you want to further customize your case, think about adding logos, engravings, or other decorative elements. When it comes to different personalization or branding, this step becomes particularly crucial.
Step 3: Prototype Development
Sketch Your Design or Use Digital Design Tools: Create a detailed sketch of your design. For more precision, use digital design tools to create a virtual model of your case.
Consider Creating a 3D Prototype for Better Visualization: Developing a 3D prototype can help you visualize the final product and make any necessary adjustments before moving to mass production. This step is crucial for identifying potential design issues and ensuring a perfect fit.
Step 4: Development of Prototypes
Use Digital Design Tools or Sketch Your Design: Make a thorough sketch of your plan. Make a virtual model of your case with digital design tools for greater accuracy.
Think About Building a 3D Prototype to Improve Visualization: Before going into mass production, creating a 3D prototype can help you see the finished product and make any necessary changes. This process is crucial for spotting possible shortcomings in design and ensuring a perfect fit.
Step 5: Choosing a Producer
Find a Reputable Silicone Product by Researching It Producer: Seek out producers who have a proven track record of creating silicone goods of the highest caliber. Go through reviews, get suggestions, and assess their prior project portfolio.
Share Your Design and Particular Needs with Others Clearly: Give the manufacturer every detail of your design, including the size, composition, color scheme, and any unique elements. For you to guarantee that your vision is specifically realized, clear communication is essential.
Step 6: Manufacturing Procedure and Molding Methods
Recognize the manufacturer’s molding method. Liquid silicone injection molding is the most widely used process for developing silicone protective cases because it enables accurate and effective production.
An overview of silicone injection molding in liquid form: In this process, liquid silicone rubber is injected into a mold, where it cures and assumes the mold’s shape. This technique works well for making detailed designs and making sure of a precise fit.
Step 7: Quality Control
Verify that the manufacturer has implemented strict quality control procedures. Throughout the production process, quality checks should be made to make sure the finished product complies with all safety and design requirements.
Actions Made to Guarantee Excellence: Producing a high-quality custom silicone case requires routine inspections, fit and durability testing, and assurance that all the specifications for design are satisfied.
These instructions will help you design a silicone protective cover that serves your functional needs and showcases your brand or personal style. To get the best results, the process—from initial design to final production—requires meticulous planning and cooperation with a dependable manufacturer.
The Manufacturing Process of Silicone Protective Cases
A precise and thorough manufacturing process is required to create a silicone protective case. Here’s a closer look at every phase:
(1) Concept and Modeling
First Draft: The first step in the process is to create a design based on the given specifications. Designers consider the dimensions and distinctive features of the device when producing intricate sketches and digital renderings of the finished product.
(2) Manufacturing A Prototype
Next, a prototype is created, frequently with the aid of 3D printing technology. This makes it possible to investigate and test a physical model of the case. Before going into mass production, prototyping is essential for finding any design flaws or necessary adjustments.
(3)Molding
Molding: A mold is made after the final design is decided upon. Usually composed of steel or aluminum, the mold is expertly crafted to precisely match the design’s dimensions and details. Throughout the production process, this mold will be used to form the silicone into the required shape.
Liquid silicone injection molding is the main technique utilized in the manufacturing of silicone protective cases.
Procedure of Injection: High pressure is utilized to inject liquid silicone rubber (LSR) into the mold. To form the case’s shape, the silicone fills the mold and flows into all of its spaces.
Setting Time: After that, the mold is kept closed for an agreed-upon period of time so that the silicone will solidify and take on the shape of the mold.
(4) Curing and Finishing
Molding: A mold is made after the final design is decided upon. Usually composed of steel or aluminum, the mold is expertly crafted to precisely match the design’s dimensions and details. Throughout the production process, this mold will be used to form the silicone into the required shape.
Liquid silicone injection molding is the main approach utilized in the manufacturing of silicone protective cases.
Procedure of Injection: High pressure is employed to inject liquid silicone rubber (LSR) into the mold. To form the case’s shape, the silicone fills the mold and flows into all of its spaces.
Setting Time: After that, the mold is kept closed for an agreed-upon period so that the silicone begins to solidify and take on the shape of the protective cases.
(5) Quality Assurance
Testing and Inspection: An essential part of the manufacturing process is quality assurance. Every case is carefully examined for flaws and put through testing to make sure it satisfies the criteria that are required.
Visual Inspection: Cases are examined to look for any visible flaws, such as dents, dings, or faults in the molding and finishing procedures.
Functional Testing: Cases are tested to make sure all ports, buttons, and features are reachable and operational, and that they specifically fit the intended device.
Durability Testing: The case is put through a battery of tests to measure its overall durability, impact resistance, and flexibility to make sure it offers enough protection.
Final Approval: The distribution of cases is contingent upon their effective completion of all quality checks. This guarantees that every product that is supplied to clients satisfies rigorous standards for performance and quality.
NEWTOP Custom Silicone ——Reliable Silicone Protective Case Manufacturer
Because of its vast experience and knowledge in the production of silicone products, NEWTOP stands out when it comes to selecting a reliable silicone manufacturer. NEWTOP has a track record of ensuring the highest quality standards by using exacting manufacturing methods and stringent quality checks. With the company’s extensive customization options, customers can easily fit products to their particular needs and tastes.
Testimonials from satisfied customers show a wealth of accomplishments and encouraging remarks, highlighting NEWTOP’s commitment to quality. NEWTOP continues to be at the forefront of innovation in the silicone manufacturing sector by utilizing cutting-edge technology. Furthermore, their committed customer support and consultation services offer priceless assistance throughout the creation process, making sure that every product is expertly crafted to exceed expectations.