Hoses are crucial components in many different applications, ranging from industrial to residential. They are used to transport liquids, gases, and other materials from one place to another. Hoses come in different types, sizes, and materials, each suited for specific applications. For instance, hydraulic hoses are used in heavy industry to carry high-pressure fluids, whereas garden hoses are used in homes for watering plants and lawns. In the automotive industry, hoses are used to transport fuel, oil, and coolant. Regardless of where hoses are used, their importance cannot be overstated. They play a critical role in maintaining the functionality and efficiency of various systems. Without hoses, many operations would come to a halt, leading to significant losses in productivity. Therefore, it is essential to ensure that hoses are well-maintained and replaced regularly to prevent leaks and other problems.
There has always been a debate between silicone hoses and rubber hoses. While rubber hoses are more commonly used and less expensive, silicone hoses are gaining popularity for their durability and resistance to extreme temperatures. Rubber hoses are more prone to cracking and deterioration over time, especially if they are exposed to heat or chemicals. Silicone hose, on the other hand, is more elastic and can withstand high temperatures without losing its shape or flexibility.
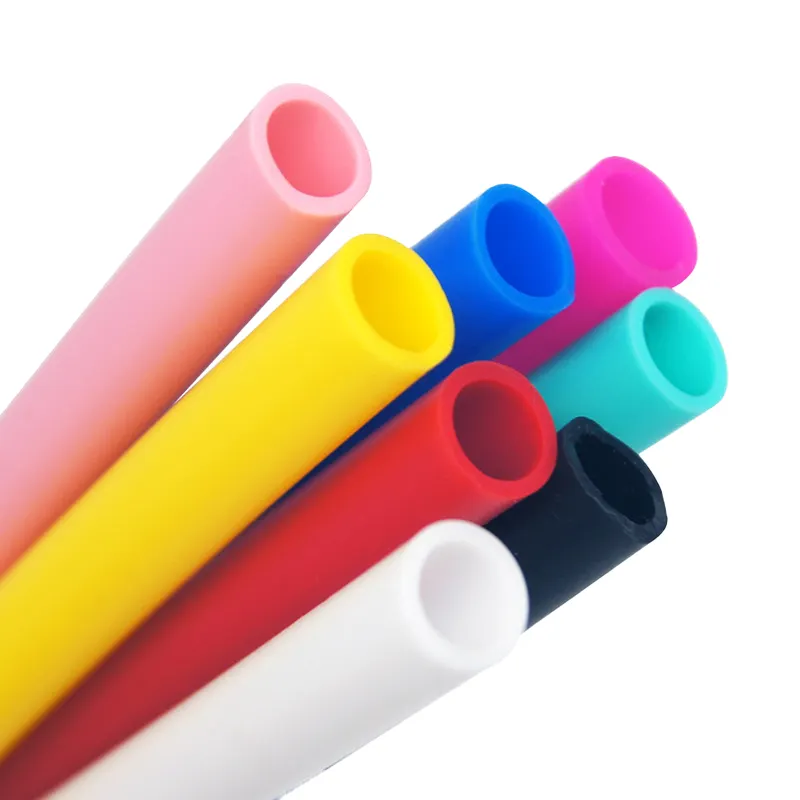
Ultimately, the choice between silicone hose and rubber hose depends on the specific needs and requirements of the application. It is important to consult a professional to determine which type of hose is best for your particular use case.
The purpose of this essay is to provide a comprehensive overview of the comparison between silicone hoses and rubber hoses. It seeks to understand how to choose a suitable hose. This investigation will not only shed light on the resilience of the silicone rubber hose but also offer insights that could be instrumental in navigating the choice of silicone hose and rubber hose.
Understanding Silicone Hose and Rubber Hoses
In the world of materials and manufacturing, silicone and rubber are two commonly used substances that have distinct properties and applications. While both are elastomers and share some similarities, they have significant differences in terms of composition, characteristics, and applications. This article aims to provide a comprehensive overview of silicone and rubber materials, highlighting their unique qualities and helping you understand how they differ from each other.
(1) Composition
Silicone is a synthetic polymer derived from silicon, oxygen, carbon, and hydrogen. It is typically made by combining silicon with methyl chloride and subjecting it to a series of chemical reactions. This process results in the formation of a highly stable and flexible material known as silicone. On the other hand, rubber is a natural or synthetic polymer derived from organic compounds, primarily latex obtained from plants or petroleum-based substances.
(2) Properties
Silicone exhibits exceptional heat resistance, maintaining its properties even at high temperatures. It can withstand extreme cold, UV radiation, and environmental exposure without degradation. Silicone also possesses excellent electrical insulation properties, making it a preferred choice in electronic applications. Furthermore, it is highly resistant to chemicals, oils, and solvents. Rubber, on the other hand, offers excellent elasticity and resilience. It has superior impact absorption and provides good frictional properties. Rubber materials can be engineered to exhibit various degrees of hardness and flexibility, making them suitable for diverse applications. However, rubber is not as resistant to heat, chemicals, and environmental factors as silicone.
(3) Applications
Due to its unique properties, silicone finds applications in a wide range of industries. It is commonly used in the manufacturing of medical devices, such as implants, prosthetics, and tubing, as it is biocompatible and does not cause allergic reactions. Silicone is also extensively utilized in the automotive sector for gaskets, seals, and hoses due to its excellent resistance to temperature fluctuations and aging.
Rubber, on the other hand, is widely used in the production of tires, conveyor belts, seals, and gaskets. Its ability to provide traction, withstand heavy loads, and resist abrasion makes it an ideal material for these applications. Rubber is also used in the construction industry for various purposes, including insulation, flooring, and roofing.
(4) Durability
Silicone exhibits remarkable durability, retaining its physical properties over an extended period. It does not become brittle or crack under harsh environmental conditions, which makes it suitable for long-term applications. Rubber, while durable, may undergo degradation over time due to exposure to UV radiation, ozone, and other environmental factors. However, advancements in rubber compounding and additives have significantly improved its resistance to aging.
(5) Cost Considerations
In terms of cost, rubber is generally more affordable than silicone. Rubber materials, especially synthetic ones, are widely available and cost-effective to produce. Silicone, on the other hand, involves a more complex manufacturing process, leading to higher production costs. Consequently, the price difference between the two materials can influence their choice in various industries and applications.
Properties and characteristics of silicone hoses and rubber hoses
Silicone hoses and rubber hoses are commonly used in various industries due to their unique properties and characteristics. Silicone hoses are known for their excellent heat resistance, allowing them to withstand high temperatures without degradation. They are also highly flexible, making them ideal for applications that require movement or bending. Additionally, silicone hoses exhibit exceptional resistance to chemicals, UV radiation, and ozone, ensuring long-lasting performance in harsh environments. On the other hand, rubber hoses are valued for their superior abrasion resistance and durability. They can handle a wide range of temperatures and are resistant to oil and fuel, making them suitable for applications involving fluids and gases. Rubber hoses also provide good flexibility and can be easily molded into different shapes and sizes. Overall, both silicone hoses and rubber hoses offer specific advantages depending on the requirements of the application, making them reliable choices for various industries.
Performance and Durability
1.Comparing heat resistance of silicone and rubber hoses
When comparing the heat resistance of silicone hose and rubber hose, silicone hose becomes the superior choice. Silicone hose has exceptional heat resistance, allowing it to withstand high temperatures without any noticeable degradation. They can typically handle temperatures ranging from -50°C to 200°C (-58°F to 392°F), and can even withstand short-term exposure to higher temperatures. In contrast, while rubber hoses also exhibit some degree of heat resistance, they tend to have a lower threshold than silicone hoses. Rubber hose typically has a temperature range of -40°C to 120°C (-40°F to 248°F), making it more suitable for applications involving moderate heat levels. Therefore, when it comes to applications that require extreme heat resistance, silicone hoses are the first choice, providing reliable performance and longevity even in challenging high-temperature environments.
2.Assessing flexibility and kink resistance
There are several key factors to consider when evaluating the flexibility and kink resistance of silicone and rubber hoses. The first is the material itself—silicone is usually more resilient than rubber, but it also tends to be more expensive. Another factor to consider is the thickness of the hose wall – thicker walls will generally provide more kink resistance, but may also make the hose less flexible overall. Finally, the design of the hose can also play a role – a hose with more curves or bends may be more prone to kinks, while a hose with a straighter design may be more flexible.
3.resistance to chemical and environmental factors
Silicone and rubber hoses possess distinct attributes in terms of their resistance to chemicals and the environment. Silicone hoses exhibit superior tolerance to high temperatures and UV radiation, rendering them ideal for applications subjected to severe environmental conditions. Nonetheless, they may demonstrate comparatively lower resistance to specific chemical agents when compared to rubber hoses. Conversely, rubber hoses generally exhibit enhanced resistance to chemicals such as acids and solvents; however, they may not withstand high temperatures or UV exposure as effectively.
4.Evaluating longevity and lifespan
Silicone hoses generally have a longer lifespan compared to rubber hoses. This is primarily due to the inherent properties of silicone, such as excellent resistance to temperature extremes, chemicals, and UV radiation. Silicone hoses are less prone to degradation, cracking, and drying out over time, which contributes to their extended lifespan. They are also more resistant to ozone, which can cause rubber hoses to deteriorate. Additionally, silicone hoses maintain their flexibility and elasticity over a longer period, reducing the risk of leaks or failure. On the other hand, while rubber hoses are durable and robust, they may experience some degradation over time, particularly when exposed to harsh chemicals or extreme temperatures. This can result in reduced flexibility, cracking, or brittleness. However, the lifespan of rubber hoses can still be significant if properly maintained and used within their specified temperature and chemical compatibility limits.
Functionality and Application
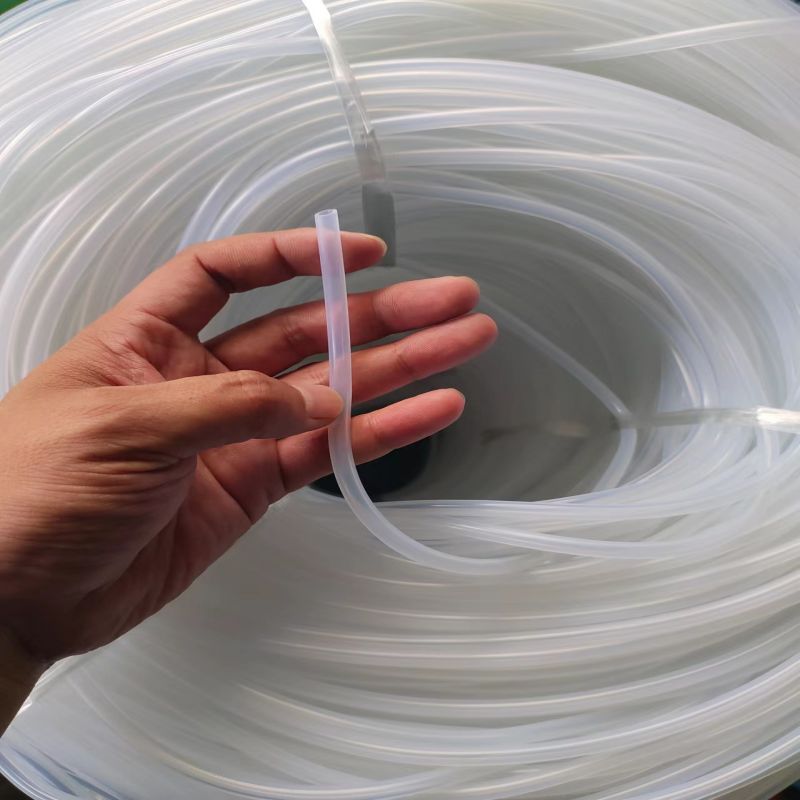
Silicone hoses and rubber hoses are commonly used in various industries for fluid transfer applications due to their flexibility, durability, and resistance to high temperatures. Both types of hoses have unique properties that make them compatible with different fluids and temperature ranges.Silicone hoses are known for their exceptional heat resistance and can withstand extreme temperatures ranging from -50°C to 200°C (-58°F to 392°F).
They maintain their flexibility and integrity even at elevated temperatures, making them suitable for applications involving hot air, steam, and coolant transfer. Additionally, silicone hoses exhibit excellent resistance to oxidation, ozone, UV radiation, and most chemicals. However, they may not be compatible with certain petroleum-based fluids, such as gasoline or oil, as they can cause the silicone material to swell or degrade over time.
On the other hand, rubber hoses offer good resistance to a wide range of fluids, including petroleum-based products like oil, gasoline, and diesel fuel. They also have moderate resistance to high temperatures, typically ranging from -40°C to 120°C (-40°F to 248°F), depending on the specific rubber compound used. Rubber hoses are commonly used in automotive, industrial, and hydraulic applications. However, they may not be suitable for prolonged exposure to extreme heat or certain chemicals, as they can deteriorate or become brittle over time.
Assessing pressure ratings and burst strength
Silicone hoses and rubber hoses have different pressure ratings and burst strengths, which are important considerations when choosing the appropriate hose for a specific application. Silicone hoses typically have lower pressure ratings compared to rubber hoses. They are commonly rated for medium to high-pressure applications, with typical working pressures ranging from 10 to 20 bar (145 to 290 psi). However, it is important to note that silicone hoses may have lower burst strength compared to rubber hoses, meaning they may be more prone to failure when exposed to sudden spikes in pressure. Therefore, it is crucial to operate silicone hoses within their recommended pressure limits to avoid potential damage or rupture.
Rubber hoses, on the other hand, often have higher pressure ratings and greater burst strength. They are available in a wide range of options to accommodate various pressure requirements, ranging from low-pressure applications around 5 bar (72 psi) to high-pressure applications exceeding 100 bar (1450 psi). Rubber hoses are engineered to withstand substantial pressure fluctuations and sudden increases in pressure without experiencing catastrophic failure.
Applications in industries such as automotive, food processing, and medical
Silicone hoses and rubber hoses find widespread applications across various industries, including automotive, food processing, and medical sectors, due to their unique properties and capabilities.
In the automotive industry, both silicone hoses and rubber hoses are utilized for coolant systems, turbocharger systems, intercooler systems, and air intake systems. Silicone hoses are favored for their high-temperature resistance, making them suitable for carrying hot air, coolant, and turbocharged air. Rubber hoses, on the other hand, are commonly used for fuel lines, brake systems, and power steering applications, thanks to their compatibility with petroleum-based fluids and their ability to handle moderate pressures.
In the food processing industry, silicone hoses are widely employed due to their excellent hygiene and FDA-approved properties. They are preferred for transferring food and beverage products, as they do not impart odor or taste and are resistant to bacterial growth. Silicone hoses are also known for their high-temperature resistance, making them suitable for applications involving hot liquids or steam cleaning processes. Rubber hoses, with their good resistance to chemicals and oils, are used for conveying non-fatty food products and other non-critical fluid transfer applications.
In the medical industry, silicone hoses are commonly used in various medical devices and equipment, such as ventilators, anesthesia machines, and surgical instruments. Silicone hoses are biocompatible, flexible, and heat-resistant, making them ideal for critical medical applications. They are resistant to sterilization methods like autoclaving and ethylene oxide (ETO) sterilization. Rubber hoses, with their compatibility with fluids and moderate temperature resistance, are utilized in medical devices where non-critical fluid transfer or low-pressure applications are required.
Both silicone hoses and rubber hoses play vital roles in these industries, providing reliable fluid transfer solutions tailored to the specific needs and challenges of each sector. It is essential to select the appropriate hose material based on factors such as temperature requirements, fluid compatibility, and regulatory compliance to ensure safe and efficient operations in these demanding industries.
Advantages of Silicone Hoses
Due to their numerous advantages, silicone hoses are often used in a variety of industrial, automotive, and medical applications. Here are some of the main advantages of silicone hoses:
High-temperature resistance: Silicone hoses can withstand high temperatures, usually between -60°C and 220°C, depending on the grade of silicone used. This makes them ideal for applications where they are exposed to extreme heat, such as automotive engines and industrial machinery.
Flexibility: Silicone hoses retain their flexibility and do not harden over time like rubber hoses. This makes them ideal for applications that require bending, such as cooling systems for cars or complex machinery.
Durability and service life: Silicone hoses have excellent aging properties and generally last much longer than other types of hoses. They are resistant to hardening, cracking, ozone erosion, sunlight, and general weathering.
Chemical resistance: They can withstand a variety of chemicals that other hoses cannot, including various types of coolants and antifreeze.
Less toxic: Silicones are generally considered less toxic and more environmentally friendly than many other types of materials. It also does not support microbial growth, making it a good choice for medical and food-grade applications.
Low permeability: Silicone hoses are much less permeable to gases and water vapor than other types of hoses. This makes them ideal for applications that require gas and moisture resistance.
Color Diversity: Silicone hoses can be produced in a variety of colors, which is beneficial for applications where aesthetics or color coding is important, such as high-end automotive or performance applications.
Vibration reduction: The silicone hose has good vibration reduction ability and can absorb the vibration and movement of machinery or vehicles.
Advantages of Rubber Hoses
Rubber hoses also have several advantages that make them suitable for a wide range of applications. Here are some of the main advantages:
Cost-effective: One of the main advantages of rubber hoses is that they are generally cheaper compared to silicone hoses. This makes them a more economical option for many applications.
Wear resistance: Rubber hoses are generally very resistant to wear, making them suitable for use in harsh environments and applications where they may be subjected to rough handling.
Flexibility: Rubber hoses are known for their flexibility. They can bend and bend without breaking, which is useful in many industrial, automotive, and home applications.
Resistance to certain chemicals: Although this depends on the type of rubber used, many rubber hoses are resistant to a variety of chemicals. They are commonly used to transport gases, water, and certain types of chemicals.
Good vibration damping: Like the silicone hose, the rubber hose also has good vibration damping. This helps reduce the impact of mechanical or vehicle movement.
Fuel and oil resistance: Some types of rubber, such as nitrile butadiene rubber, have excellent oil and fuel resistance, making them suitable for applications that come into contact with such substances.
Pressure handling: Rubber hoses can usually withstand a lot of pressure, which is critical for applications such as electric washing machines and hydraulic systems.
Easy connection of accessories: Rubber hoses can be easily combined with various types of hose accessories, making them versatile.
Are Silicone Hoses Better Than Rubber Hoses?
“Are Silicone Hoses Better Than Rubber Hoses?” For this question, the answer is: The superiority of silicone hoses over rubber hoses depends on the specific application and requirements. Both silicone and rubber hoses have their strengths and applications. Silicone hoses are known for their exceptional heat resistance, longevity, and versatility in extreme temperature conditions. They are well-suited for demanding applications where reliability and performance are critical factors. On the other hand, rubber hoses offer good durability and versatility at a lower cost, making them suitable for general-purpose applications.
All in all, the choice between silicone and rubber hoses depends on the specific needs of your application. Consider factors such as temperature requirements, environmental conditions, and the type of fluids or gases being transferred. By understanding the properties and capabilities of each type of hose, you can make an informed decision and select the option that best suits your requirements. Remember, whether you choose silicone or rubber, it is essential to ensure that the hoses you purchase meet industry standards and are of high quality to ensure optimal performance and longevity.